Uncovering Hidden Losses in your Operation
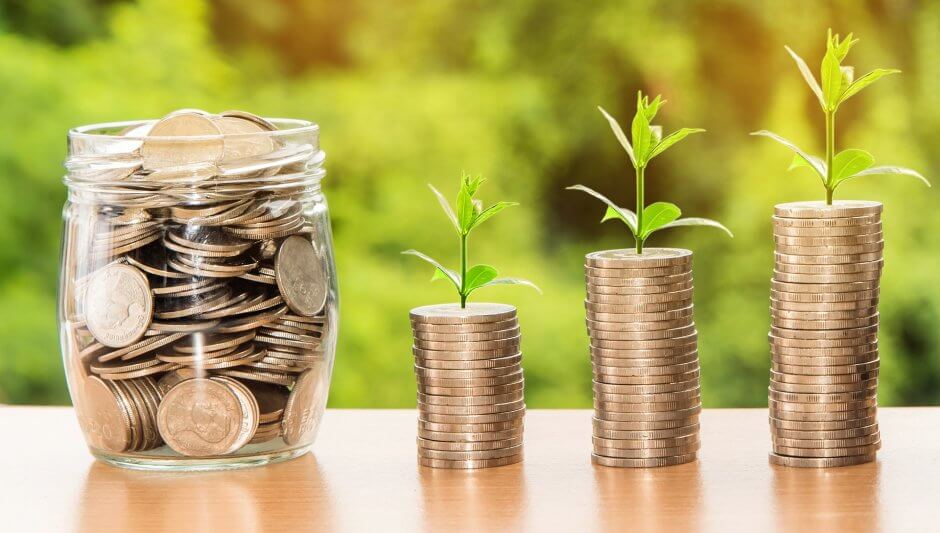
As a manager of a facility, you may find yourself looking at your revenues and wondering why numbers are not adding up as you had initially projected. I will be highlighting common losses frequently missed as well as expenses to consider lowering. Please note that this is not a complete list of items that can be identified, and it is something that is continually evolving with technological advancements and social changes.
A great starting point is appraising your raw material, which is likely part of your major costs. You can save on costs regarding moisture by setting a purchasing standard of 10% moisture content with your raw material suppliers. If a supplier sells you beans with moisture higher than this, they should discount the price proportionally with the excess moisture. Remember, about 50% of pre-extruded moisture will be flashed off during the extrusion process, and too much residual moisture left post-extrusion greatly reduces shelf-life and quality of the finished product.
The same logic applies to foreign matter like stones. Extruding stones will result in a significant cost to you in terms of parts longevity, finished product quality, and best practices. To avoid this, proper raw material cleaning is essential. To lower costs and save money, take a sample of each order delivered, establish the percentage quantity of foreign matter and discount this proportionally from the agreed upon price. Remember to include the cost of cleaning; particularly in instances where this must be outsourced or where the supplier had the service available to them for a fee.
Pilferage is yet another concern. This is not only an issue that applies to our customers in frontier markets, but also in emerging and developing economies. The first step is to develop a clearly defined process map along with signed off and recorded accountability in the procurement chain. Who bought what, when, from who, and from where? What was produced and where was it sold? Any movement of raw material and finished product must be recorded in a manner that ensures traceability to the initial source.
The final major concern I will be discussing is electricity costs. With electricity, there are two areas to watch: power factor correction and motor utilization. Look at your power bill to see if you are charged a power factor surcharge penalty. If so, installing a capacitor bank is a priority. I have seen instances where this penalty constituted 20% of the total power bill. Correcting the power factor ratio remedies this immediately.
To address costs with motor utilization, consider taking the following steps. The first is to install overload circuit breakers. Our motors have a 15% overload service factor allowance on the motor plate, this means you can set your breakers at around 10% above the full load amps indicated on the motor name plate. It would be practical, however, to consult with our service department before doing this. The next step is to load your main motors as close to maximum amps as possible during operation. However, extruders that are feeding presses cannot be ran at full load due to the maximum press amps being the limiting factor.
Remember that hidden in every cost center within your operation is an opportunity to save or become more efficient. If you are interested in learning more on these issues, please contact our Service Department.