Start-Up Time
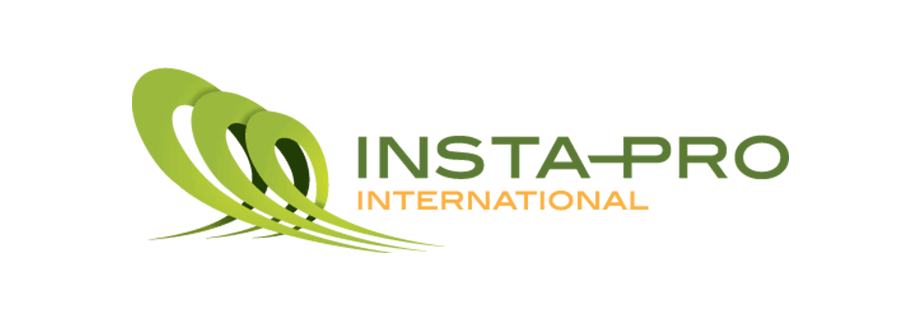
After doing hundreds of equipment start-ups over the last 30 years, I’m here to tell you it can be a wild time that comes with emotional ups and downs and no lack of stress. It doesn’t have to be that way. I’m going to discuss some of the ways to try and avoid the start-up being a negative experience.
The first and easiest thing to do is to make contact with establish a relationship with the guys in the Insta-Pro shop. There is a wealth of information and years of experience that comes with the purchase of your Insta-Pro equipment, and it doesn’t cost a thing besides your time.
- Oz Grimm and Jim Little both have operating experience and are familiar with virtually all related equipment and processes.
- Jeff Vaske builds all of the extruders and calibrates the electrical controls and sensing equipment. He knows extruders top to bottom and can assemble one blindfolded.
- Bill Jensen is our oil press doctor. He knows every part on every press that goes out of here. I think he even names some of them!
- I’d like to say I have seen most everything, too, in my experience of traveling to customer sites.
So get our phone numbers, emails, Skype, whatever else, and give them to your contractors, installers, electricians and plumbers. The lack of communication amazes me that we have with new owners prior to start-up. There’s no such thing as a dumb question, especially if you’re new to the process. Sometimes a simple question can avert a problem down the line.
Read on to see a few more topics to discuss about start-up:
Be realistic about installation and start-up scheduling – we all know too well the urgency related to getting the equipment up and running. Most installation schedules are based on a best case scenario. The problem with that is 99% of the time, it never happens. Some minor delays and unexpected problems always seem to creep up. Depending on the size of installation, these can result in delays of days if not weeks. Nothing turns up the stress meter like having product promised to a customer on a certain date and no product in the bins.
The result is pressure on everyone. In my experience, this is when mistakes are made, corners are cut, small details are forgotten, or temporary measures are taken. This usually translates into problems later on, which only add to delays. When figuring the timeline for installation, give yourself a buffer of typically a week to 10 days, depending on the size of the installation.
Scheduling the Insta-Pro Technician for start-up – our technicians are very busy. They are scheduled tight and travel the world. They also cannot afford to sit around for two or three days while the installation is completed. Prior to start-up, you will receive a Start-up & Training Request Form with questions regarding the status of the installation and requesting photos and signatures. Completion of the request form is required before schedules are set and travel arrangements are made.
Time spent on a start-up is calculated by amount and kind of equipment being started. Delays of 1 or 2 days are common and almost expected. We request 2 weeks notice, prior to the desired start-up date. I know this can be tricky as most people are still in the installation process. My advice is to contact Jim Little or Ray Goodwin who schedules the start-ups about a month ahead of when you estimate you will be ready. He can answer any questions you have at that time. This also gives us a heads-up to tentatively set time aside for your project. Weekly contact from this point on will give us a progress report and allow us to schedule accordingly.
Be patient – typically, a start-up consists of starting at one end of the production line and tuning and fixing problems until you get to the other end and all works in harmony. What may seem like big problems are routine when it comes to start-up.