Which Cooler is Right For You? Part 1
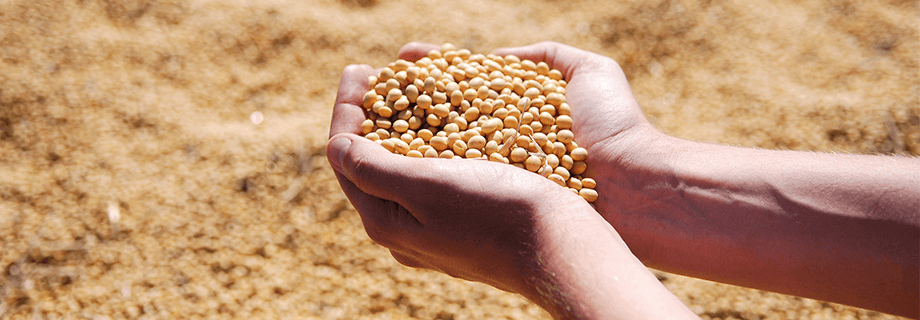
When using high shear dry extrusion for oilseed processing, the final product typically only needs to be cooled. This is the case when making either full fat soya (FFS) or our ExPress® soy meal. There are various ways to cool product to safe levels. The following are brief descriptions of popular cooler styles along with their advantages and disadvantages for cooling extruded soy products. It should be noted that coolers are designed for one purpose: to cool product. While there is some drying effect, this is not the main purpose.
Rotary drum cooler
A simple choice is a rotary drum style cooler. This is the type we offer for lower capacity products. These have a large, cylindrical vessel that rotates at a very slow rate. The vessel has internal vanes or arms that scoop up product at the bottom, but due to the slow rotation, the product falls down on itself when it nears the top of the rotation. An air system draws ambient air into the end of the vessel and, much like a counterflow cooler, forces air across the product in the opposite direction of conveying. These types of coolers are very simple to operate and are generally used in smaller plants due to simplicity and ease of operation.
COUNTERFLOW COOLER
Image courtesy of Bliss Industries
Counterflow coolers get their name from the interaction between the product being cooled and the air that cools it. These are cylindrical in shape and operate in a vertical process. In the picture, the product comes into the top of the cooler in a metered way (small, red rectangles). There are a series of doors on the bottom that open and close on a timer or based on levels in the tank. As product enters the vessel, the level inside of the cooler builds up. A fan and cyclone system draws air into the vessel and through the product. Based on either a time interval or bin level, the bottom louvers/doors open and release a certain amount of product and then the whole process starts over again. The air direction is opposite of the product flow direction and runs counter to it, hence this cooler’s name.
These coolers are popular in the industry and typically the first choice for cooling needs of larger production rates. They can work on a large variety of granular products and work especially well for FFS or ExPress® meal and other extruded products. They have a floor space advantage since they are vertically oriented, so large capacities do not require the same footprint as a similarly sized drum cooler.
The right cooler for your plant will depend on what you are processing, the capacity, floor space, and capital. There is the ability to upgrade down the road, but always be sure to take into account any future expansion plans. Coolers can generally run at reduced capacities fairly well, so if you do plan to expand, investing in a larger cooler up front may be the way to go. If your product requires both drying and cooling, then a dryer/cooler is the best option. This will be discussed in part two.