The New Model 8800 Oil Press: Feature Highlights
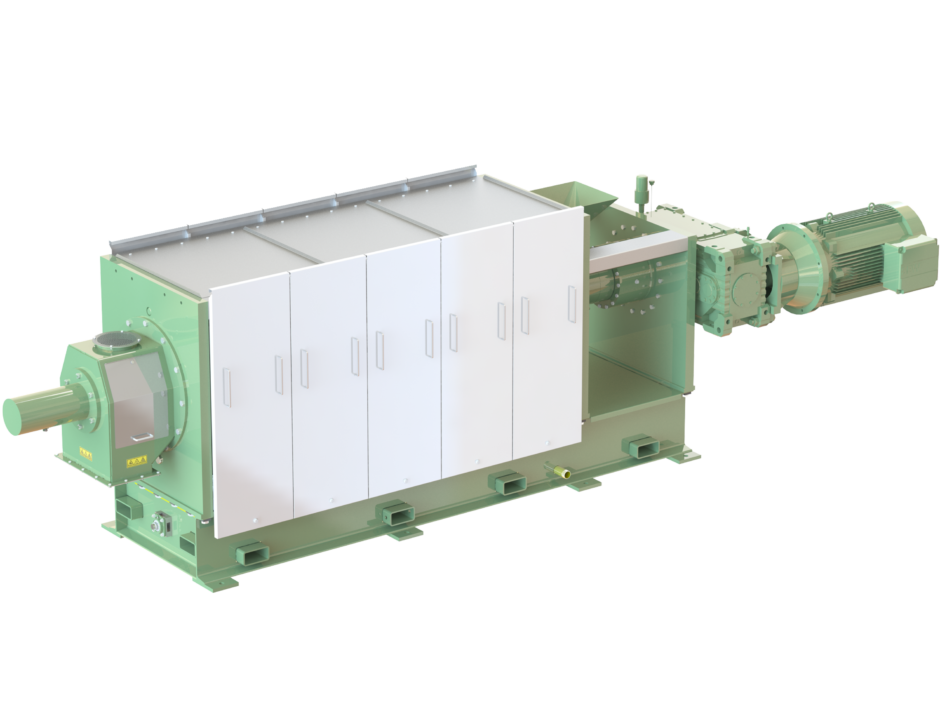
Insta-Pro has a long history of providing world-class oilseed processing solutions. This includes our ExPress® System which maximizes oilseed product value, coupling high-shear dry extrusion with mechanical oil pressing. Insta-Pro’s largest 1:1 extruder to press solution was previously a 2 TPH ExPress® module. In order to meet increasing demand for high-capacity solutions that require less space, we released the 4 TPH Model 9000 Extruder in 2019. This was the start of a complete 4 TPH ExPress® module featuring a 1:1 extruder-to-press configuration.
Insta-Pro is preparing to complete this solution with the quickly approaching release of the new 4 TPH Model 8800 Oil Press. The 8800 press is a scaled-up version of Insta-Pro’s existing 2 TPH Model 5005 Oil Press. It maintains the same high-quality construction and exceptional processing efficiency while providing several exciting new features.
Four key new features of the Model 8800 Oil Press include the following:
- Direct gear drive:
Using a direct gear drive configuration eliminates the additional energy and power losses associated with a chain or belt driven unit. Furthermore, there are fewer wear parts and reduced maintenance. The direct gear drive prevents the use of a top or side mounted motor minimizing the overall machine width and height. This also allows for a shorter base frame and eliminates the need for a separate motor mount which reduces material, weight, and cost.
- External thrust housing with reverse-operation capability:
The 8800 press features a newly designed bi-directional external thrust housing. This allows the shaft to be rotated in either forward or reverse direction. Rotating the shaft in reverse direction helps to break up material and empty the cage without needing to split the cage open. This increases the ease of cleanout procedures and reduces downtime. When operated in reverse direction, product exits the machine through an easy-to-use cleanout door located on the inlet housing.
- Cast cage assembly:
Manufacturing of the press cage has been upgraded from a fabricated process to a casting process with machined features. Using a cast assembly saves time and improves overall manufacturability. It also produces a more consistent part. This leads to a final cage assembly that is better performing and more economical.
- 10:1 cage length to cage diameter ratio:
The 8800 press features a 10:1 cage length to cage diameter ratio which is higher than the 8:1 ratio used for Insta-Pro’s smaller 5005 press. The higher ratio allows the machine to handle more capacity while maintaining the same level of oil extraction as the 5005 press.