Automation & Process Control
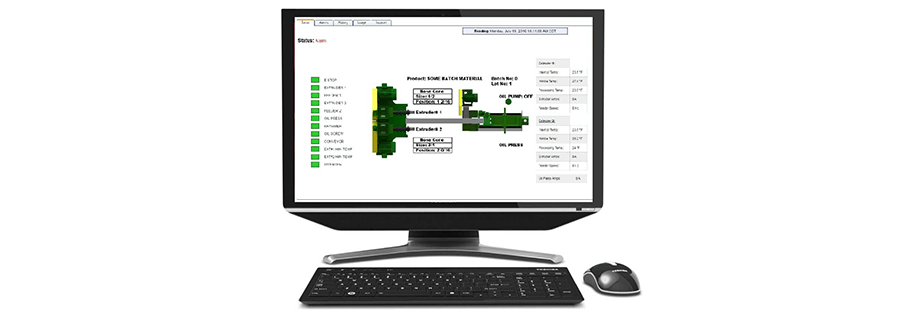
There’s an old quote that says “you don’t know where you’re going until you know where you’ve been.” While this may be philosophical, it can be relevant to your business. Many times we are involved in troubleshooting and problem solving issues in production. A customer may call us and say that they cannot maintain or reach a certain temperature or nutritional specification or that parts are continually breaking. Our normal process is to begin asking a series of questions to help determine the root cause. While this works, it is a reactive approach. What if you could be proactive and avoid these issues altogether?
Measure It
How can you improve things if you cannot measure them? Let’s take something simple like moisture content of soybeans. You can rely on your supplier to tell you that the moisture of the beans is 12%, but can you assume this is the case throughout your entire process? Customers have called to ask for help when running the ExPress® process because they are having a high level of solids coming out of their press. Our first question is usually “what’s the moisture content of the incoming soy?”. Some customers are fortunate enough to have a lab on-site, but some do not. Having a way to measure this and other important metrics, such as nutritional content, is extremely beneficial. There are affordable NIR options, like our Portable Ingredient Analyzer (PIA), that allow for on-the-spot readings to let you know your process is within specifications. This can save costly recalls down the road.
Control It
Automation is the new normal. Even in lower capacity plants, there is typically some level of automation. The level of this is an important factor in plant process design. Automation increases efficiency, reduces labor costs, and can increase safety depending on the process. The “human” side of things is taken away, so errors can be reduced. Along with measuring key processes within your system, automating them may be another way to avoid “surprises”. Even if it is something that is not required at first, at some point, everyone will likely consider it. Automation can be done in stages, but it is typically easier to start with it rather than retrofit afterwards.
Monitor It
Measuring and controlling are great preventative measures, but in order to truly capitalize on these, you need to have a system to continually monitor and check your process. Regular sampling on set intervals will allow you to start tracking your data. From this data, you can establish correct operating zones.
The extruder is a fairly manual machine, but new advances such as our Production Intelligence Program (PIP) allow customers to remotely monitor their system and get alerts if problems arise. A manager can get alerts via email or text for things ranging from maintenance reminders to out-of-range processing temperatures. More sophisticated systems even allow video monitoring of lines which can prove invaluable for remote troubleshooting.
The Future
Controlling your process is the key to a successful business. Measuring performance is a key to growth, but also a key to improvement. There are several tools available to make your business successful and reduce the amount of time it takes to gather this data. Using tools such as the Portable Ingredient Analyzer and the Production Intelligence Program and knowing how to use them will save you time, improve efficiencies, and make you more profitable in the future.