Value Stream Mapping: What and Why? Part I
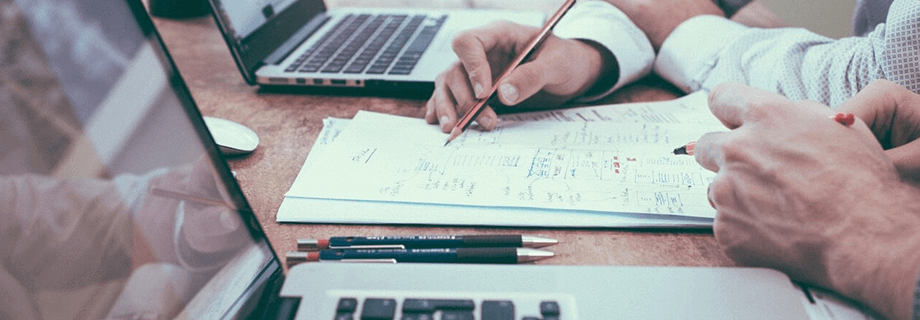
Lean manufacturing is still a big part of business, but it has become second nature in most places and lost some of its original effect. Buzzwords and phrases like kaizen, six-sigma, and “low-hanging fruit” are commonplace today, almost to the point of being cliché. This doesn’t mean their practices have become obsolete, however. An effective tool to use when trying to discover inefficiencies in a process is value stream mapping. This process requires you to follow your company’s goods through their entire process flow within your organization. While this may sound easy, correctly doing it requires the help of the entire organization and can help uncover significant, sometimes enlightening, opportunities.
What is Value Stream Mapping?
At its core, value stream mapping is nothing more than a process flow chart. This doesn’t have to be limited to a product-based manufacturing system. Any process can be mapped, but your definition of “product” may vary. In some places, it may be the exchange of information. In others, it’s a good or commodity-based product in which materials are received into a company, processed, and then shipped to the customer. The major checkpoints in the system are those in which “value” is added to the product. Again, your definition of “value” will change depending on the product, but the ideas are the same. Every time there is a change of state of the product, that process is noted. You will note all of these checkpoints during the event.
Value stream mapping typically takes place over a dedicated amount of time. These are not small events that can be done in an afternoon. To do it right, you may need a full day on smaller processes or a solid week for larger processes. These are cross-functional events where every team in the organization is involved. The value stream of a product should involve every department since every department is what keeps the organization moving.
Why map?
We all as business people want our businesses to operate in the most efficient manner. We want to shorten timeframes and lower costs. Value stream mapping was designed as a way to visually see the flow of a product in an organization since people generally understand information better this way. The most important thing a value stream map event does is highlight problem areas or inefficiencies in an organization. As you follow a product’s path within your company, you will likely uncover a lot of areas to improve upon. Multiple handling steps, redundant information and unnecessary processes are just a few of the items that show up. It is a very powerful tool that anyone can use to highlight problem areas so they may be addressed.
As you can see, the value of stream mapping is significant to every organization to continue improving. To learn how to apply this at your own organization, check out next week’s blog in part II.