TOM D WIP – Lean Manufacturing’s Enemy
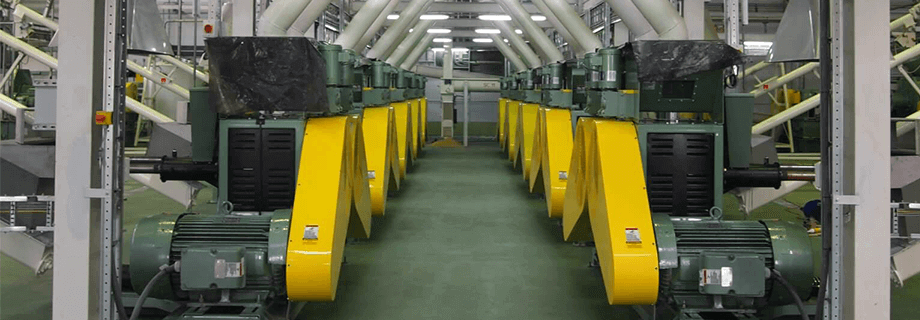
Lean manufacturing is a concept that has been around for a while and has become the go-to buzzword over the last several years. Every company wants to create a “lean” culture that promotes efficiency, productivity and minimal errors. How do you go about this in your own plant?
At the cornerstone of most lean cultures is the Toyota Production System (or “TPS”). This methodology has been used in countless manufacturing settings and can be applied virtually anywhere. A key concept with this is waste reduction, which is referred to as “Muda” in the TPS. Every process can be classified as either “value-add” or “non value-add” and deciding what processes fall into each category will help your facility become more efficient. While it is true that eliminating wastes will create a more efficient process, where does one start? A simple way to think and evaluate each process goes as follows.
The 7 Types of Waste
There are several common phrases for this, but taking the first letter of each waste gives the following pneumonic: TOM D WIP. By evaluating each process, one can identify sources of inefficiency and correct them. Every process should be evaluated for value-added and non value-added benefits.
T – Transportation
How many times is product moved during the process? Every time something is transported, the risk of it becoming damaged, lost or worse, increases. The less the product is moved, the better. An example of this is post bagging. Ideally after bagging, product could go directly to shipping. Any storage stops present an opportunity for product to be damaged.
O – Overproduction
Overproduction has a tendency to hide problems. Large batches are usually run in order to make up for lost time with excess amounts being made to account for production issues. If a recall occurs, the batch size is now potentially larger than it could have been, resulting in more discarded product. Another problem occurs if there is a momentary issue in production (mis-fed material, surging, etc.). This could go undetected due to the large amount of product until it reaches the customer.
Overproduction reduces the amount of control one has over the process and usually leads to another form of waste: excessive inventory. It can snowball from there: you now have to find room to put everything which can lead to delays and potential defects because items are getting in the way.
M – Motion (excess)
How far away does product need to travel to be processed next? If the next process is a long distance away, extra time is required before product can be processed. Very long conveyor lengths or excessive distances between machines are likely causes. This can applied to operators, too. As an example, if an operator needs to monitor production speed and also operate a bagger, there could be excessive walking involved. Perhaps redistributing workloads or even hiring extra help will increase efficiency and reduce wait times for this process.
D – Defects
Any defective product is obviously a waste. A reduction of defects is an automatic boost in efficiency. Defects either require rework or discarding, both of which cost extra time and money. There are some process-specific things that could be causing defects such as over-heating or poor handling of pellets, but these are likely caused as a result of the wastes shown here. If the actual production seems correct but issues still exist, defects may be a by-product of other wastes.
W – Waiting
As the adage goes, “time is money”. The longer things take to produce, the more money is spent on them due to operational costs. Waiting occurs when there is not a steady production flow. Any product waiting to be processed is taking up space. This is usually present in batch-type systems. A reduction in waiting allows the process to run smoother since it reduces production surging.
I – Inventory
What happens when you have too much product? Storing excessive amounts of product is usually unnecessary. This takes up space and can make moving within the plant difficult. Work-space is a premium these days and the more efficiently it can be used, the better. Inventory needs to be evaluated and assessed to make sure the items being stored make sense. Do you have a stockpile of parts that only get used once in a great while? Perhaps these can be moved in favor of more processing space or is needed for higher-turnover items which can help response time to customers.
P – Processing (excess)
Over processing involves adding more to the product/process than necessary. Why dry a product to 5% moisture when 8% will do? Is it necessary to have 13 vitamins when the customer only asked for 11? When evaluating over processing, one has to weigh the cost to the benefits. If drying or processing below a certain point is extra assurance or a marketing strategy, the cost of this needs to be considered against the operational costs in order to justify it. If these are done to compensate for other production issues, fixing other forms of wastes is a likely (and better) use of resources.
What can I do?
No process is perfect, but the fundamental idea of continuous improvement should always be present. There are always ways to improve and become more efficient. A great place to start is to write out every process step in detail, including cycle time on a note card, one process step per card. Depending on how large your facility is, this could take several note cards! Using cards is a visual way to understand if there are wastes in the system. You can then reorganize processing steps or evaluate them to see if they are necessary or not. In the end, you may find you can gain efficiency for free.